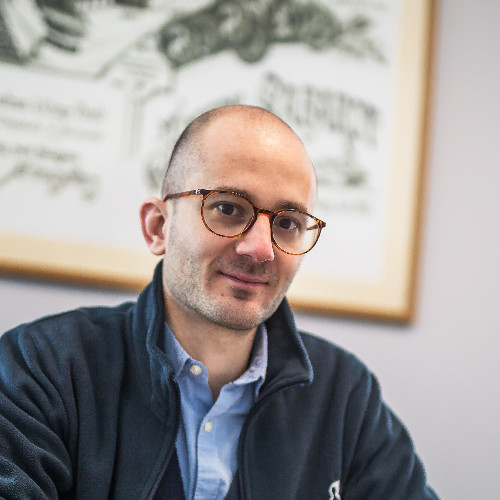
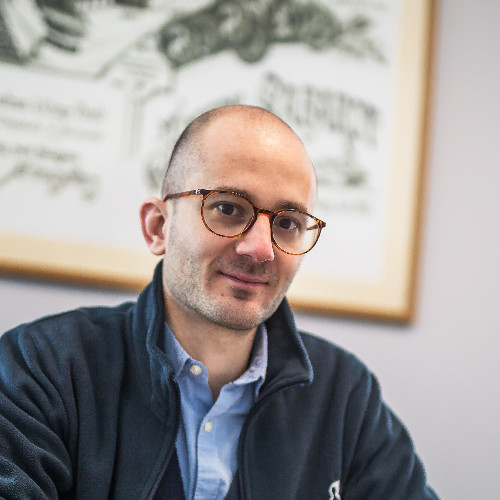
The family firm, Sabarot, a specialist in pulses, cereals, seeds, mushrooms and snails since 1819, is ideally positioned in a booming market undergoing major transformation…
To face up to the issues of increasingly complex and challenging demands, Thomas Morin and Florent Collange, Sabarot’s Industrial Director and Technical Manager respectively, have been on the look-out for an exerpt consultant on industrial processes in this field to oversee its future development.
The collaboration with Igenium, the engineering services company, began with a recommendation. Contact was made to arrange a visit to the industrial site in Puy-en-Velay and to conduct a technical audit of the facilities. As Thomas Morin relates, “We needed a solid assessment of our industrial resources. We had to understand how to go about modernising the site while taking into account the obsolescenceof certain equipment. Our ambition to double our capacity, especially in lentil sorting, meant that we needed real industrial vision.”
A pre-engineering phase, followed by a more detailed one, to help our industrial vision
The audit phase took two months and included three areas on which used to model every aspect of industrial information: mechanical, wiring and automation. It involved the input of a team of experts working solidly for five days. The team included:
The investigation took us back to our archives to examine technical data sheets from twenty-five years ago. As Florent Collange explains, “This phase of the audit enabled us to retrieve factual data, establish accurate readings and tap into automation to get a better understanding of the active programmes. One of the most unexpected challenges was human. Indeed, we had to create conditions in which everyone could express their opinion and reveal the key data in their possession. A mine of constructive, valuable information for what came next.”
A reasoned presentation of the pre-engineering report of the project highlighted a number of facts: the current situation, the industrial vision for the future and the potential solutions to achieving our objectives. While the maintenance audit made it possible to identify critical situations and define the technical perimeter. Certain parts no longer existed and, at times, it was necessary to wait three months to obtain the replacement components. A short-, medium- and long-term action plan was drawn up to replace certain machines and/or keep them in working order.
Doubling production capacity with the help of efficiency curves
Compiling all of this data provided an opportunity to suggest efficiency curves, which make it possible to pinpoint existing bottlenecks and resize the system in line with the results observed. “Depending on the machine, we examined the product transfer system and spotted any differences according to process. Efficiency curves are very powerful projection tools”, says Thomas Morin enthusiastically. With the major issues involved in increasing production capacity, the initial rough draft of the project provided answers to a number of questions:
As a result of this key phase, Igenium was able to provide Sabarot with an industrial vision for the future that incorporated innovative solutions capable of supporting the growth of a flagship of the French agrifood business.
3D modelling helping to promote the industrial project
“Sabarot made the decision to place its trust in Igenium’s expertise to head up the project and set up the new facilities. Their role was to see if all of the objectives were met and to keep a very, very close eye on the budget,” Thomas Morin points out.
The fact that there were no up-to-date drawings owing to the age of the machines meant creating new drawings from scratch with the help of 3D modelling. Those drawings provided a better understanding of the space. They also helped to simulate various scenarios to feed back into the project. Providing the project with real added value, the 3D modelling of the buildings resulted in a considerable time saving and a better grasp of the space.
The key figures involved in modelling the buildings in 3D
A considerable amount of work was then undertaken to draft the specifications for the factory upgrade. This work meant defining the number of lots and the subdivision of each lot, and then determining the number of service providers required. Each lot corresponded to a specific profession (civil engineering, machines, electricity, automation, industrial data processing, disassembly and reassembly) and was tweaked to suit the industrial processes required and what the project needed to guarantee its success.
Specific specifications were drawn up for each lot: the special administrative clauses (or CCAP in French) and the special technical clauses (or CCTP in French). It was all put out to tender among potential suppliers and partners for each lot to allow them to put in their bids to take part in the project. Igenium then took charge of analysing and comparing the various bids and selecting and approving the service providers in tandem with Sabarot. On average, three service providers were selected for each lot. A site visit was arranged for each of them before working out the design of the bid.
On-site support from Igenium and its teams
The suppliers’ bids were examined and any technical clarifications made in order to spot any divergences in relation to the specifications and better understand the reasons for such differences.
Igenium also handled project follow-up, coordinating the suppliers in implementing any solutions necessary, such as operations on site and site preparation for the installation of the machines. Igenium found solutions for Sabarot and took any decisions necessary to deal with last minute glitches.
Site follow-up was arranged to coordinate activities and suppliers and obviate any undesirable incidents. Igenium handled the formalities of acceptance of the work and ran tests on and started up the production tools, while ensuring that the set objectives were met. The mission was broken down into various phases and payment made according to progress. Considerable transparency, communication and stringent project management were applied at all times.
ROI measured and analysed throughout the project
“Once the objectives of the specifications had been met, we examined the results and analysed the reasons for any divergences. The project, initially scheduled to complete in three years, was finally delivered in two. We worked hard to ensure that the project came in on time and on budget”, recalls Technical Manager, Florent Collange.
Once the project framework has been established and approved, it is time to get things moving and work proper can get under way. This third phase marks a very important step: implementation of the various solutions selected. To optimise the work and enable the technical teams to progress according to plan, various provisions have to be made while ensuring that production does not come to a complete standstill. The lentil production factory comprises various workshops: reception, cleaning and packaging. It was therefore decided to stagger production accordingly by building up stocks in advance. This makes it possible to start work while respecting three objectives:
It is time well spent to get the job done in complete safety. At the end of May 2023, the very last mechanical component will be completed and the project can be finalised. Igenium, a veritable virtuoso when it comes to organisation, provides ongoing follow-up over the period in order to anticipate any departure from the original perimeter.
Production capacity doubled
The solution provided consisted of modernising the factory and replacing five machines dedicated to lentil sorting and processing, processes which are now faster and fully optimised. The objective is achieved. By improving performance from two tonnes of lentils sorted per hour to four, Sabarot has seen its production capacity doubled and the quality of its sorted products improved.
Until now, the facility was not automated at all. Now, with the help of Igenium, intelligence has been added to the process. Digitisation of the system has been completed, as has the replacement of any obsolete electrical components and machines. It has improved visibility throughout the factory. Control is more accurate and checking enhanced with the help of supervision of the value chain in Sabarot’s sorting facility.
A centralised display is now available on a 53-inch touch screen and on online industrial tablets for the operators.
As Thomas Morin and Florent Collange conclude, “Igenium has given us a lot of help from a technical point of view about controlling the business of sorting and, indeed, about the job itself. Immense support was provided during the entire period we spent thinking about the project, compilation of the specifications and consultations with suppliers. In following up with us in this way, Igenium provided stringency, method and job-related expertise in a holistic manner.”
Whether you have a question, a query or a proposition, we would love to hear from you.
Fill out our contact form and we will take it from there!