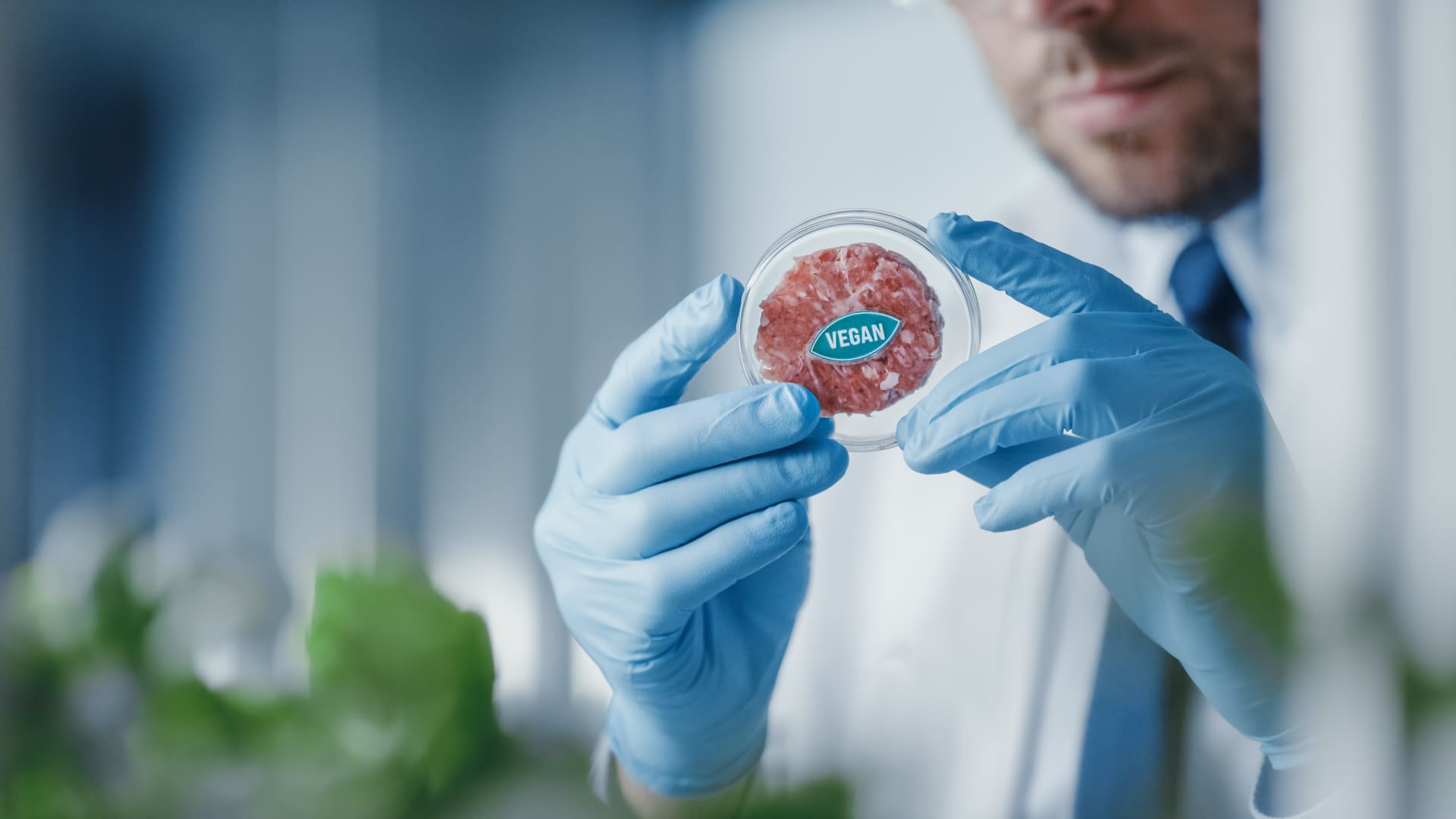
Gain in line efficiency: optimize your Premix stations!
At Igenium, we didn’t invent the powder. However, we do know how to optimize its production. Here are some explanations.
If you are not familiar with the term Premix® dosing station, you should know that most of the products you use in your daily life come from it. In theory, its use is simple: it is a device where different types of powder are mixed together. In practice, it involves complex mechanisms designed to meet very high safety standards. And that’s where Igenium comes in.
Whether it’s powdered cake mixes, flour, infant milk or premixes for the pharmaceutical or chemical industries, let’s face it: powder is everywhere in our lives. If you never realized it before, it’s simply because the issues related to their use are locked up to the extreme.
No smoke and mirrors, only high standards
Mixing powders is not a matter of chance. The dosing preparation station must be optimized to ensure perfect traceability of the product that passes through it. In terms of machine cleaning, the same applies: various mechanisms can be considered depending on the products being processed: allergenic or non-allergenic products, water-sensitive products, etc.
Another detail, and not the least: when handling powders, there is also a risk of explosion; the installation must imperatively meet the safety standards (ATEX).
At Igenium, we constantly recommend that these issues be considered during the installation of the station.
Cleanability is as much about human accessibility around the machines as it is about the cleaning recipe to clean a process. In addition, the installation must be designed to limit all potential dust: the stakes in terms of hygiene and cross-contamination can be high. We are here to advise you in this maze of standards and to offer you flexible solutions to optimize your processes: turn the constraints into a quality supplement for your product!
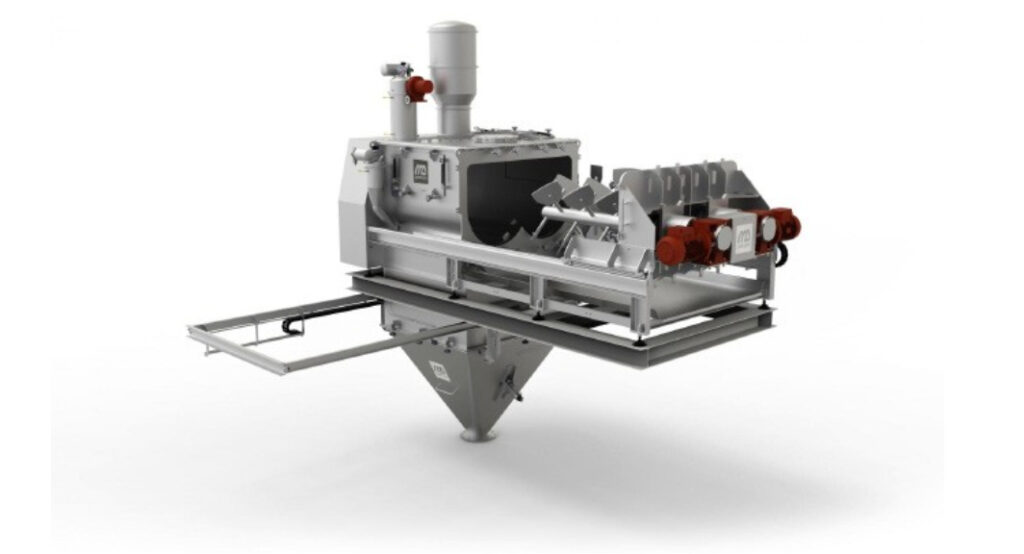
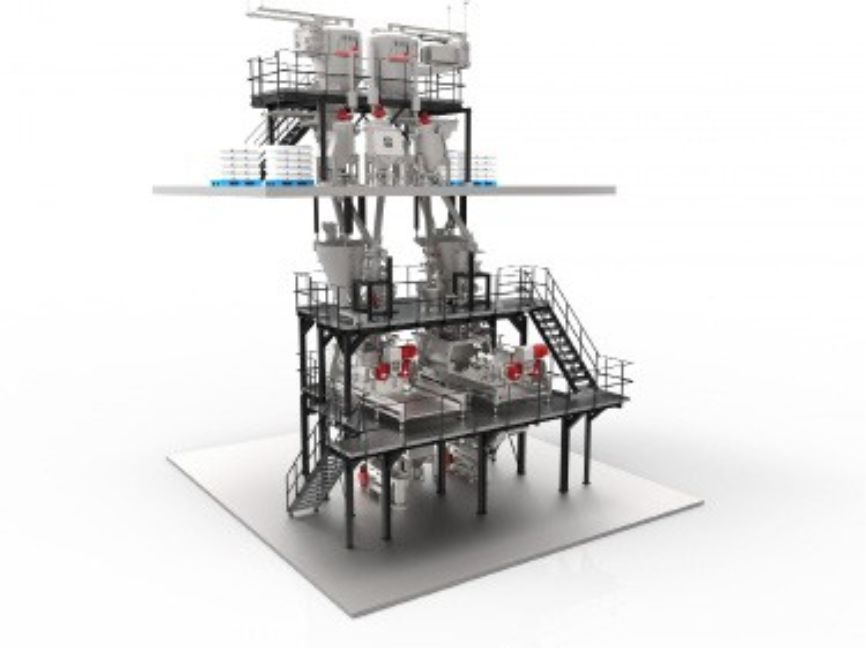
Introducing smart industry into your tailor-made processes
Aware of the technical specificities, Igenium provides you with expertise and advice based on the best practices of the industry: avoiding cross-contamination, perfecting cleanability and work ergonomics as well as product packaging.
Our aim: to design the installation that will save you time, anywhere in the world. Every customer has a different problem: that’s why we believe in haute couture rather than ready-to-wear. The result: line efficiency that makes a difference.
Because a good example is worth a thousand words, feel free to watch this Deps video: the behind-the-scenes of this egg powder production unit reveals a highly complex installation that was entirely custom-made, in partnership with Dinnissen mixers. The basic machine is standard, but its nesting is far from it.
The good news? These optimizations can be applied to a new premix station as well as to the retrofit of an existing installation. Move to Industry 4.0 and 5.0: think Igenium!
Ready to add intelligence to your automated processes and traceability? What if we reinvented the powder to achieve performance in production and quality? Contact us!
Our tailor-made support consists of 6 phases:
Phase 1 – Identifying the goals: providing advice and assistance in drawing up the preliminary drafts. (PPS): Preliminary project summary and (PPP): Preliminary project proposal
Phase 2 – Drawing up specifications: providing advice on and drafting specifications
Phase 3 – Comparing offers: providing advice and assistance in the preparation of order files
Phase 4 – Assisting in the decision-making process: drafting a support document on potential investments
Phase 5 – Providing support on the project: assisting the project owner or project manager
Phase 6 – Assisting in the development and coordination: assisting the project owner in developing the plant.
Related Insights
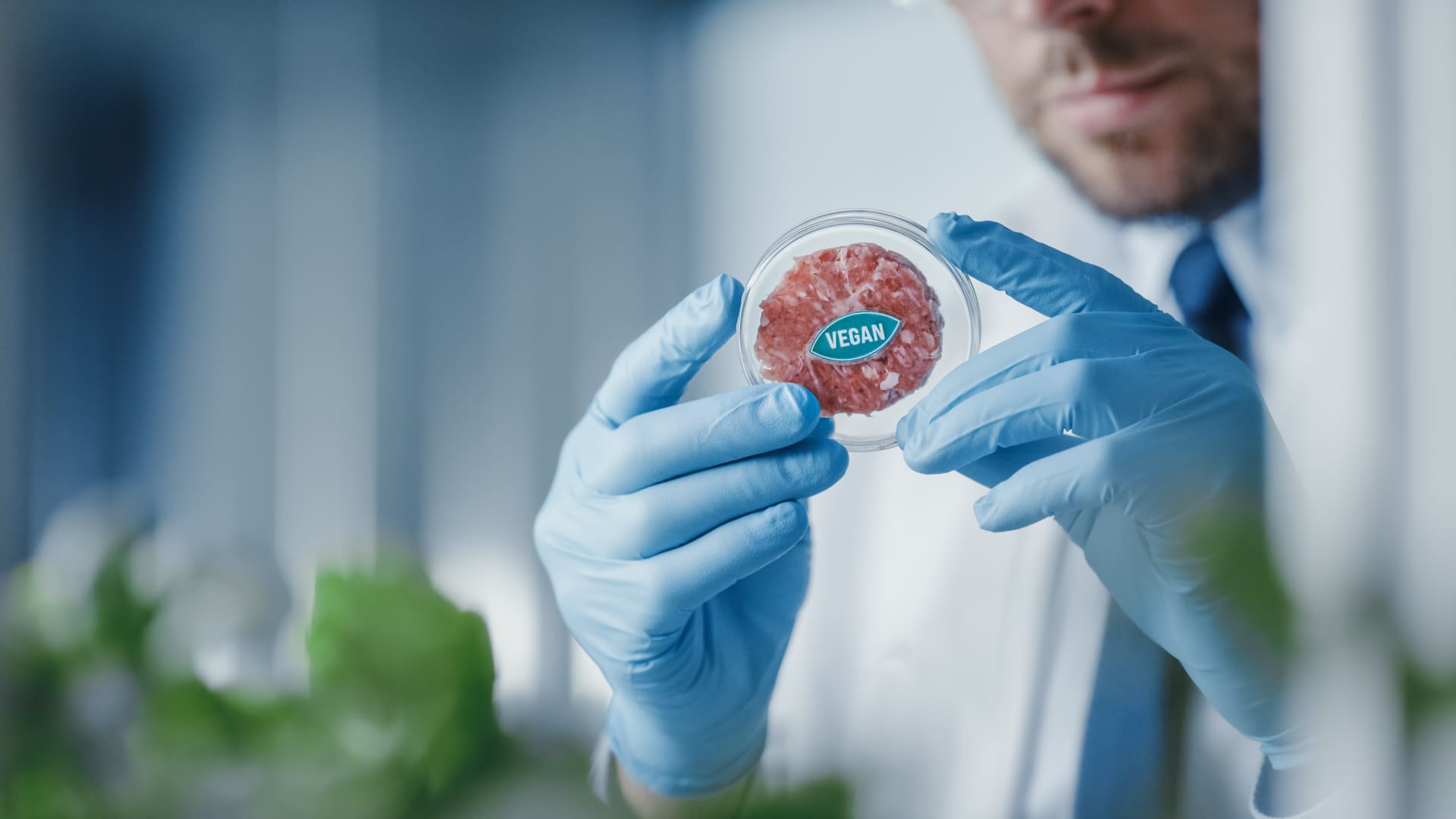
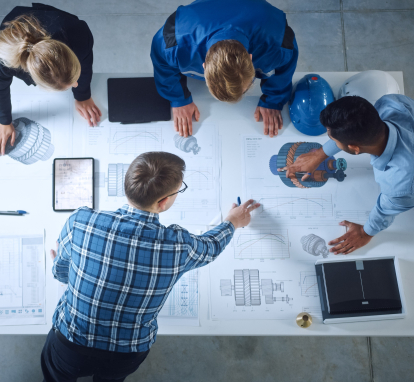